Ryukyu Lacquerware, Okinawa’s native lacquer craft
See, touch, and use genuine Ryukyu-lacquered tableware
The fine art of lacquering was originally introduced to Okinawa from China in the 14th century. Since then, Ryukyu lacquerware’s long history has been rooted in Okinawa’s subtropical climate and culture. The local craft is a type of Japanese lacquerware, with distinctive decoration techniques and craftsmanship that use natural materials from the islands. Several lacquerware shops in Okinawa offer visitors a personal experience of this rare craftwork.
History of Ryukyu lacquerware
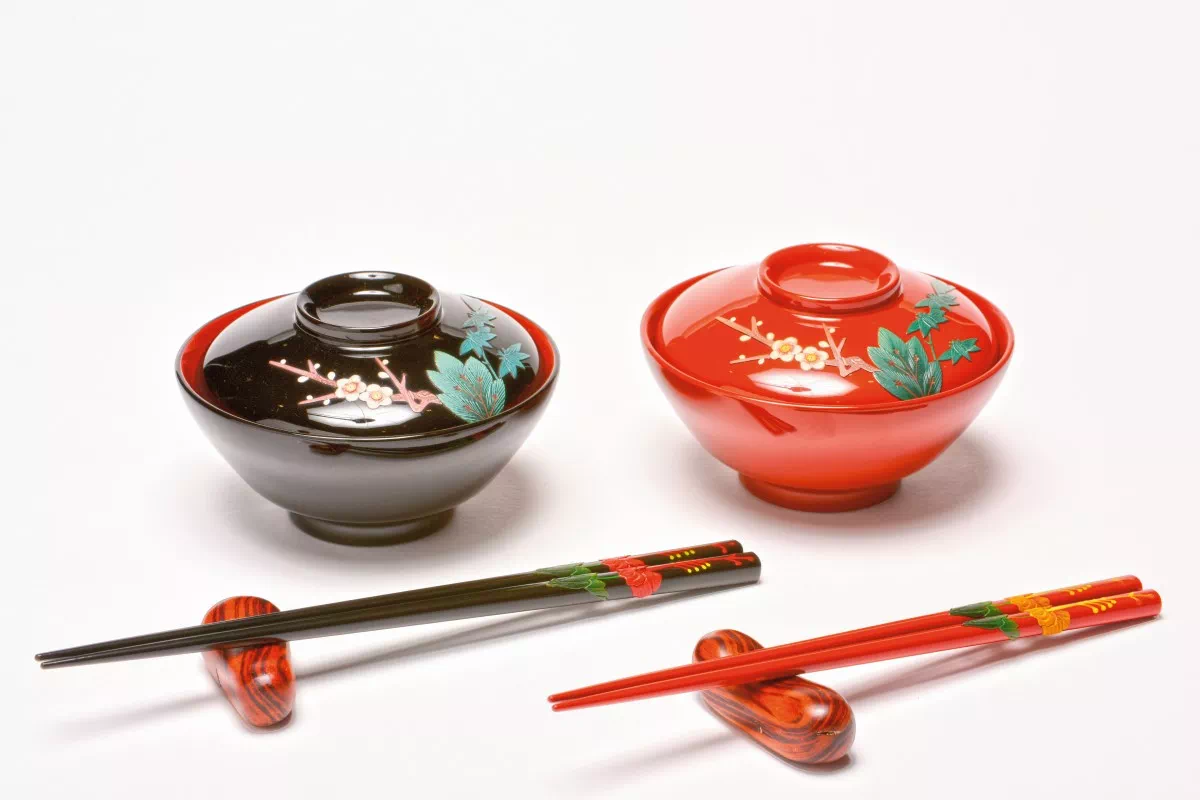
Ancient lacquered items excavated in Okinawa date back to the 13th and 14th centuries, when lacquer-coated items and lacquer-decorated necklace beads were often used in Ryukyu rituals and ceremonies, especially in places connecting people and gods.
The Ryukyu Kingdom also enjoyed prosperous diplomatic and commercial relations with China, so local artisans imported Chinese lacquering techniques. During the 15th and 16th centuries, the Ryukyu king offered ornate lacquerware as gifts to China’s emperor and ambassadors.
After Ryukyu came under control of mainland Japan in 1606, the kingdom contributed lacquerware to Japan’s Tokugawa shogunate while retaining Ryukyu lacquerware’s unique characteristics.
Since 1879, when the Ryukyu Kingdom was finally abolished, Ryukyu lacquerware has become increasingly produced by private workshops and Okinawan lacquerware companies as contemporary tableware and souvenirs for the general public.
Ryukyu lacquerware characteristics and preparation
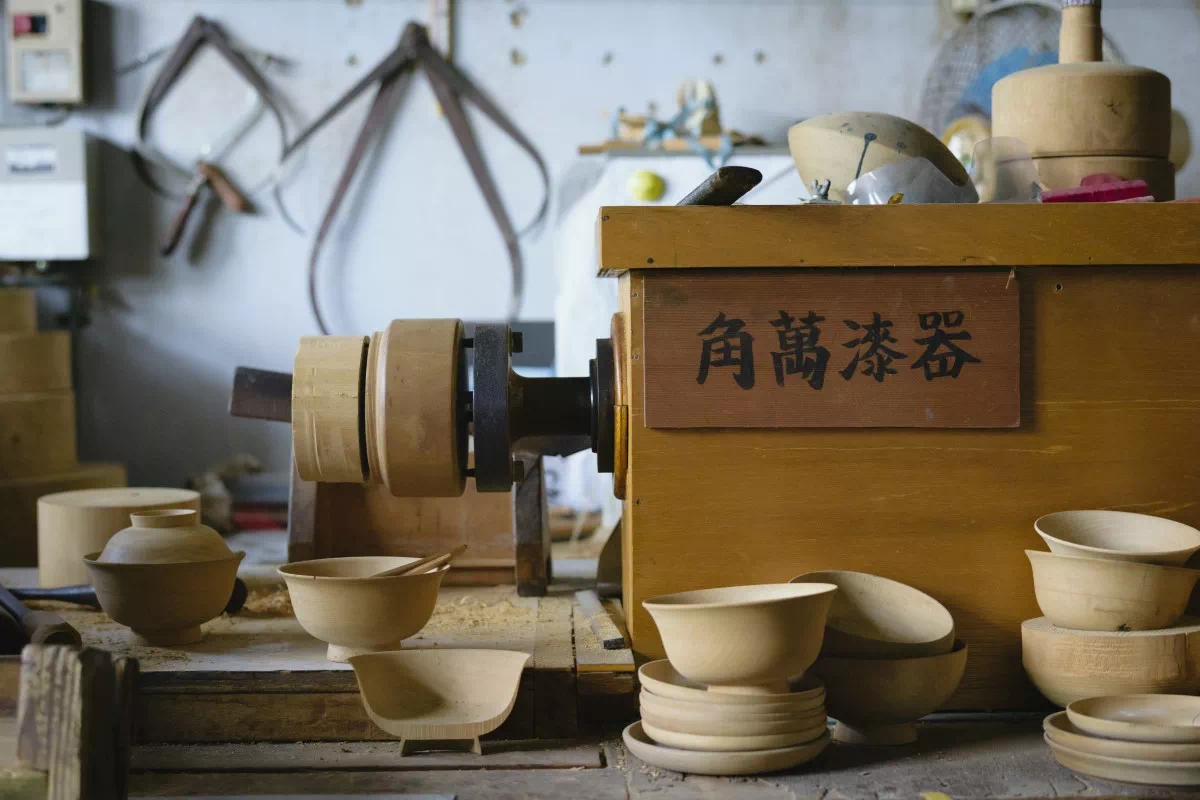
Ryukyu lacquerware is characterized by a rich color contrast between vermilion and black, as well as its distinctive decoration techniques.
Okinawa’s environment is ideal for making lacquerware. For example, during the coating process, the sun’s strong UV rays make vermilion particularly vivid. Moreover, generally speaking, drying means maintaining a low humidity level, but on the contrary, Okinawa’s high temperatures and humidity are well suited for drying lacquerware.
Ryukyu lacquerware uses local deigo and shitamaki trees, both finely-grained woods that are highly resistant to deformation. The long preparation process involves felling and drying the trees for one to five years before they can be sanded. Then areas that are likely to crack or deform due to knots or annual rings are hollowed out or shaved down. Carved or hollowed-outed areas are filled in with a mixture of deigo wood powder and lacquer and left to dry.
Ryukyu lacquering process
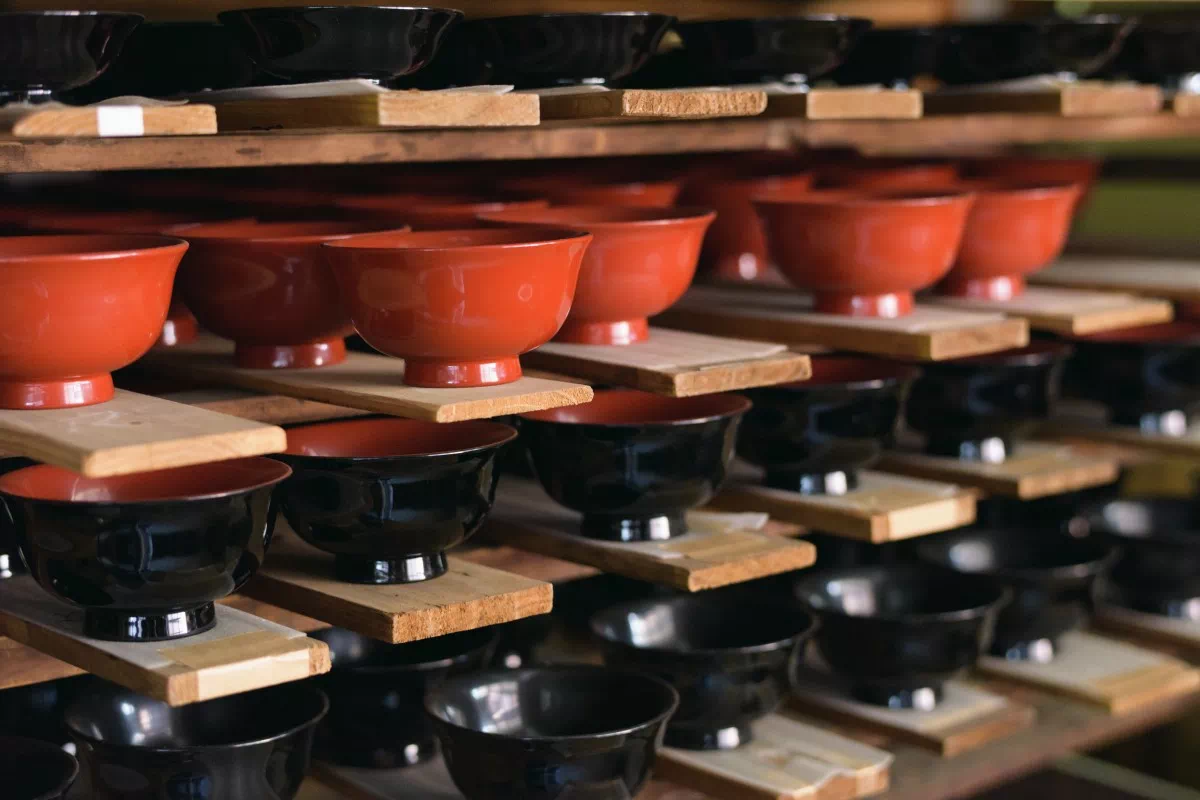
The lacquering process begins with applying the base coat, traditionally a mixture of lacquer and fine-grained niibi (Okinawan sand) and kucha (mud). The ware is then polished to refine its texture and shape, and then dried for several weeks. This initial process is repeated as many times as necessary. Next, fine holes and scratches are filled in to match the finishing coat, which is usually black or vermilion. Once dry, the ware is polished again as the lacquerer examines its surface meticulously with both eyes and hands.
Finally, the defining topcoat is applied. The mixture for the colored lacquer varies depending on the season, temperature, and weather conditions, according to the artist’s expertise and intuition. Any dust particles and air bubbles are removed with a fine needle, and the lacquer is left to dry again.
Decorative techniques of Ryukyu lacquerware
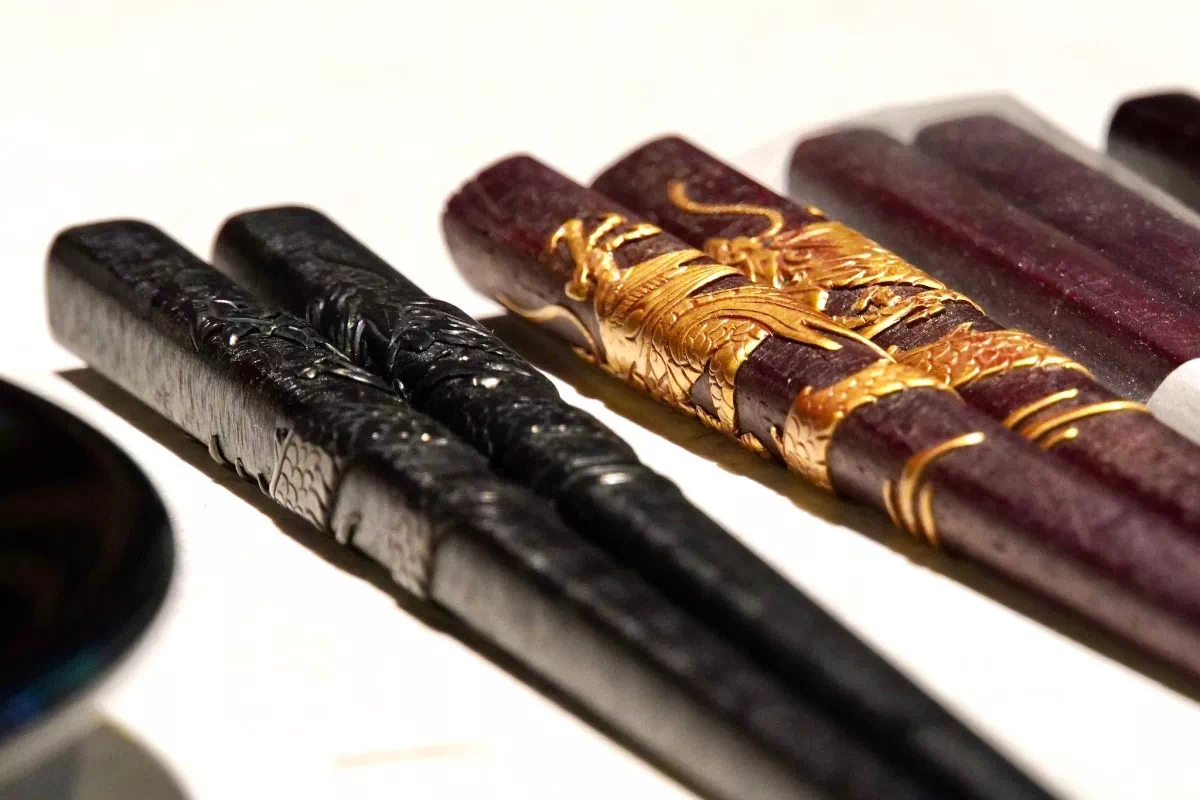
The last step is applying the decorations to the lacquered surface. Three main techniques distinguish Ryukyu lacquerware.
The most common is tsuikin, where lacquer is mixed with pigments to form a paste then spread into thin layers, cut according to the design, and pasted directly onto the lacquered surface to create a three-dimensional effect.
The raden technique refers to pasting or inlaying designs made from iridescent turban shells and abalone shells that are polished and cut into various designs.
In the chinkin technique, a pattern is carved into the lacquered surface with a blade, and lacquer is rubbed into the carved grooves. Then gold, silver, or other foil or powder is pasted onto the lacquer.
Other techniques include haku-e (foil painting) and maki-e (sprinkled painting) to express rich colors.
Ryukyu lacquerware gallery and workshop
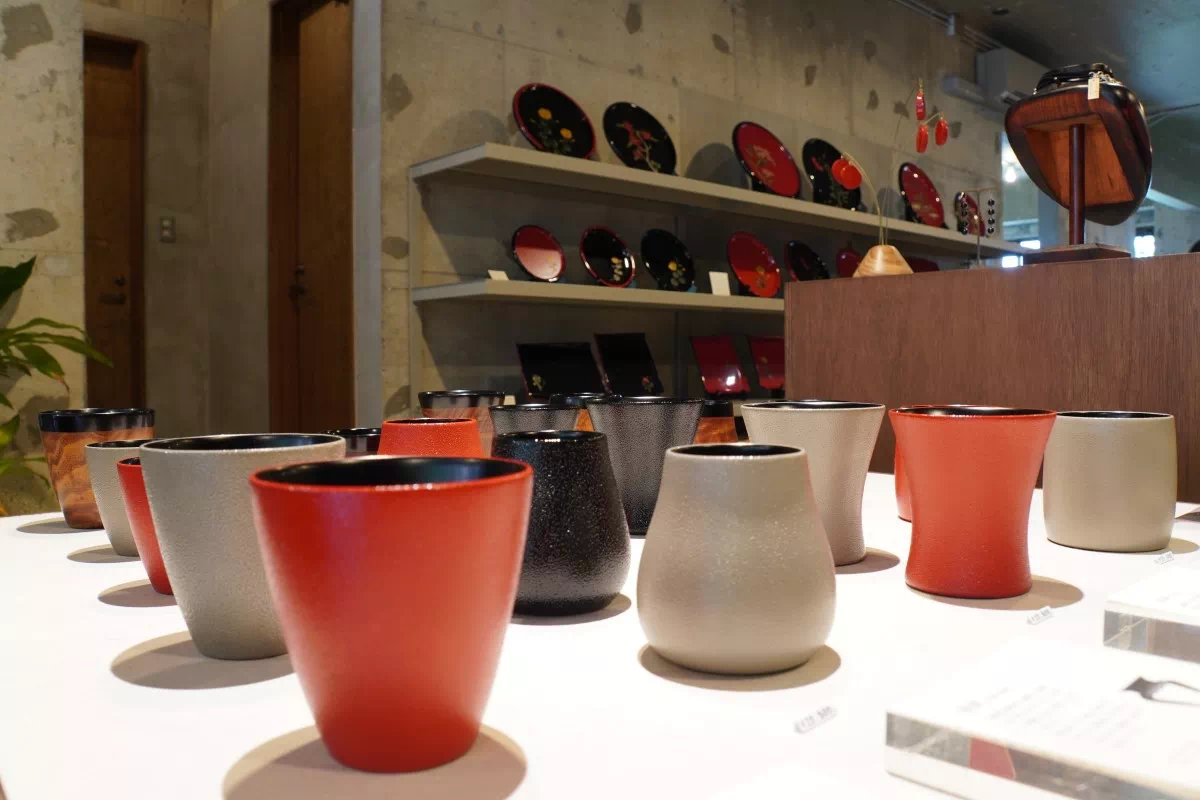
Kakuman Shikki is one of the oldest and most traditional lacquerware shops in Okinawa, originally established in Wakasa, the archipelago’s only lacquerware town in the early 20th century. Their new shop in Naha is located just steps away from Shuri Castle. One of the shop gallery’s featured pieces is an ornate box, on which iridescent dragons are inlaid against a shiny black surface.
The lacquered wares are dried and finished on-site in the upstairs workshop, including a conditioning room with precisely regulated humidity and temperature. A young lacquer artist shows us different stages of lacquer work in progress, which she follows from start to finish. As a former art student, she chose to pursue lacquerware precisely because of this long and thoughtful process, which carries on the tradition of a native Ryukyu craft.
In December 2022, Kakuman Shikki opened a dedicated gallery cafe to serve drinks to visitors on genuine Ryukyu lacquerware. This is a unique opportunity to see, touch, and use lacquerware – not just as delicate art objects, but as stylish contemporary lifestyle items.
While the company also sells lacquerware for everyday use or as souvenirs, its core mission is to preserve and promote the traditional techniques of Okinawa’s own Ryukyu lacquerware, as the oldest and most established lacquerware company in the Ryukyu Islands.
Learn More
- Ryukyu Kakuman Lacquerware *only in Japanese
Text by Cherise Fong
Cherise Fong is a devoted bicycle traveler and eco-writer currently based in Tokyo.